La impresión 3D sube al espacio
Catec y Airbus han desarrollado en Sevilla piezas para cohetes con esta tecnología
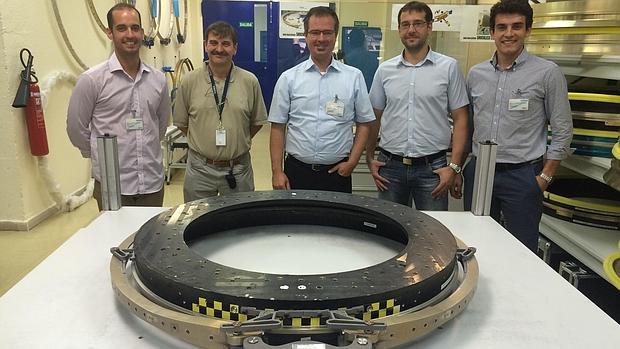
La impresión 3D está considerada como una de las herramientas de la economía del futuro al nivel de la robótica. Esta tecnología permite mandar una orden de pedido y recibir la pieza hecha en sus tres dimensiones, saltándose los pasos de la cadena de producción convencional.
Sus usos son múltiples y sorprendentes. Desde casas, a comida, todo puede «imprimirse» con este método también denominado fabricación aditiva . Las máquinas, aunque aún no se han popularizado, cada vez son más accesibles. Alguna de las que ya se venden caben en la palma de la mano y pueden comprarse en el supermercado y montarse como un mecano.
Siguiendo esta onda imparable, el Centro Avanzado de Tecnologías Aeroespaciales (Catec) ha conseguido desarrollar en sus instalaciones del Parque Aeronáutico de La Rinconada en Sevilla ( Aerópolis ), componentes y estructuras de vuelo aptos para integrarlos en lanzadores espaciales , a partir de la impresión 3D.
Tras dos años de investigación, este centro tecnológico andaluz, en colaboración con , ha conseguido un hito mundial en un trabajo para la Agencia Espacial Europea ( ESA ): fabricar y validar completamente en su centro de Sevilla un sistema de separación de fases para el lanzador espacial Arianne V , que hace que se separen dos secciones del cohete en vuelo . El fin último es hacer viable su implantación en los vehículos de nueva generación, como el futuro Arianne 6, que podrán estar operativos en el año 2020 .
Dentro de esta línea de investigación para demostrar que las piezas fabricadas mediante impresión 3D son válidas para volar, Catec también ha conseguido buenos resultados en el desarrollo del soporte donde se introducen los cables y se encauzan en una trayectoria dentro de cohetes espaciales. En este caso, el diseño se ha desarrollado para el lanzador europeo VEGA . La ventaja es que los soportes, que se fabrican en aluminio, aportan mayor rendimiento que el que se consigue a través de procesos de mejora en el diseño e ingeniería utilizando los métodos convencionales.
En concreto, los avances han permitido reducir la masa de este conector en un 62,9%, tras un proceso de optimización topológica. Mediante esta técnica se ha logrado una reducción de 0,285 kilos en el peso de la pieza , lo que se puede traducir en un ahorro de costes, en términos de carga de pago, de más de 5.000 euros por unidad, según estima el equipo que ha llevado a cabo este trabajo.
Con estos desarrollos, Andalucía pretende situarse en una buena posición de partida en la fabricación aditiva dentro de un sector, el aeroespacial , en el que aún no está madura esta tecnología.