La industria del corcho sale a flote destapando su savia innovadora
El sector explora nuevos territorios para afrontar los efectos de la fitóftora y la falta de rentabilidad de su lenta producción
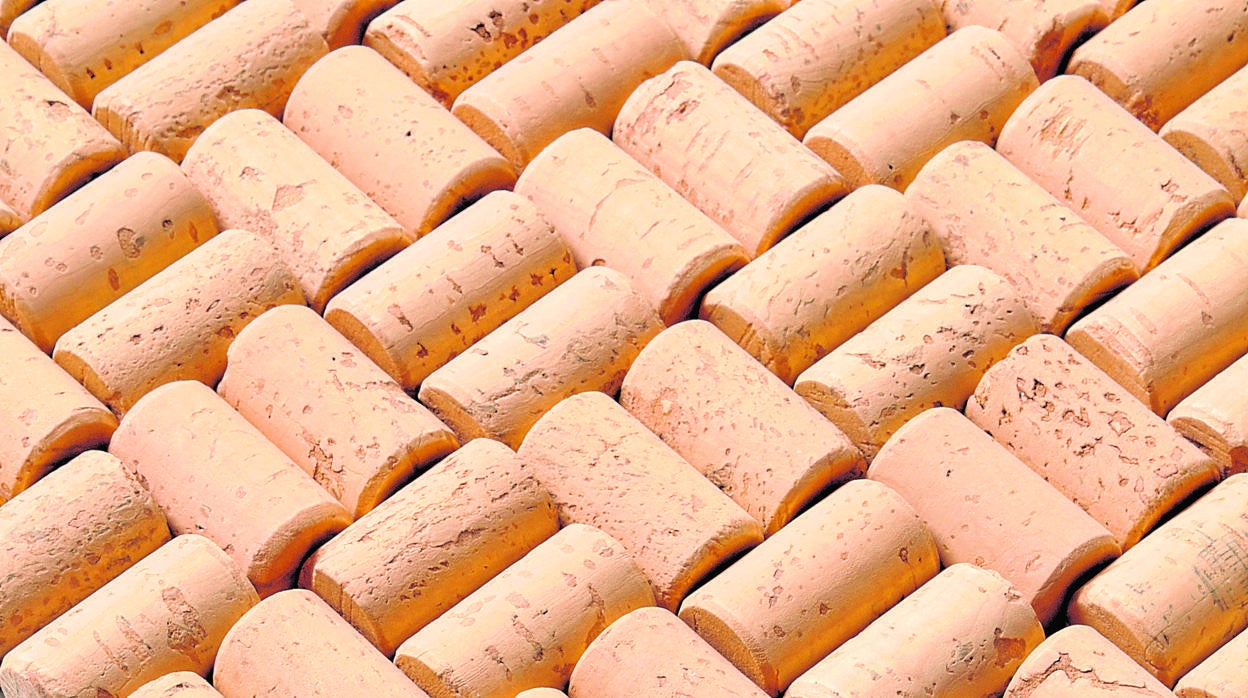
Aunque el corcho se usa fundamentalmente en el mundo del tapamiento (el 80%), con vinos y cervezas de calidad, espumosos e incluso algunas bebidas de alta graduación, su capacidad para intervenir en otras industrias como la construcción, la automoción o la naval abre un nuevo campo de posibilidades.
Es un producto con características probadas como aislante térmico y acústico, resistente y ligero, impermeable, elástico e ignífugo. Además su producción no genera contaminantes. Portugal es la mayor productora del mundo . Le sigue España, pero a considerable distancia.
El corcho se reinventa, tanto en la dehesa extremeña como en la andaluza o en zonas de Cataluña, para afrontar los efectos de la fitóftora y de la falta de rentabilidad de su lenta producción . También afecta el hecho de que algunas bodegas opten por la silicona o el plástico para la elaboración de tapones. En busca de nuevos horizontes, surgió Adicork , un proyecto encabezado por investigadores de la Universidad de Cádiz, con el apoyo de la Consejería de Agricultura de la Junta de Andalucía.
Fabricación aditiva
El proyecto Adicork, como explica Sergio Molina , catedrático de Ciencia de los Materiales e Ingeniería Metalúrgica e investigador principal del proyecto, «está desarrollando materiales compuestos de base termoplástica que incorporan corcho y otros aditivos , que han sido sometidos a un procesado que les capacita para su uso como material para procesos de fabricación aditiva de gran formato».
Hasta ahora han conseguido desarrollar más de 20 materiales y 40 diseños y prototipos. Se han identificado los sectores en los que tienen más potencial los materiales y prototipos desarrollados . «Algunos de estos sectores son el naval, aeronáutico y aeroespacial, automoción, ferroviario, mobiliario (urbano, hábitat, parques infantiles), náutica deportiva y recreativa, así como en construcción», relata el catedrático de la Universidad de Cádiz.
El mundo de la construcción ofrece varias posibilidades al corcho como las ya conocidas del parqué o el revestimiento de paredes, señala Ramón Santiago Beltrán , técnico en Subericultura del Instituto del Corcho, la Madera y el Carbón Vegetal (Iprocor), entidad adscrita al Cicytex (Centro de Investigaciones Científicas y Tecnológicas de Extremadura): «Hasta ahora la utilización era un tanto exclusiva, centrada en países nórdicos, Estados Unidos y Japón. Pero ahora se le ven otras ventajas. Hay un proyecto piloto en un barrio de Cáceres donde se está usando corcho para mejorar la eficiencia energética de viviendas ».
Uno de los objetivos del proyecto Adicorki, declara Molina, es «implantar la I+D+i en un sector poco desarrollado tecnológicamente , para abandonar la estrategia de solo producir y comercializar la materia prima, para fabricar productos elaborados de mayor valor añadido mediante la utilización de nuevas tecnologías».
La innovación también se aplica a los métodos de recogida. Apunta Ramón Santiago que en este terreno «lo más novedoso son las nuevas tecnologías en el descorche , como la máquina Coveless C18 , que regula el corte automático del corcho, o las tenazas corcheras eléctricas, que complementan el trabajo de la máquina que corta corcho en árbol. La tenaza ahueca y facilita el desprendimiento de las planchas entre sí y del alcornoque. Por último, una palanca tecnológica completa la operación del descorche».
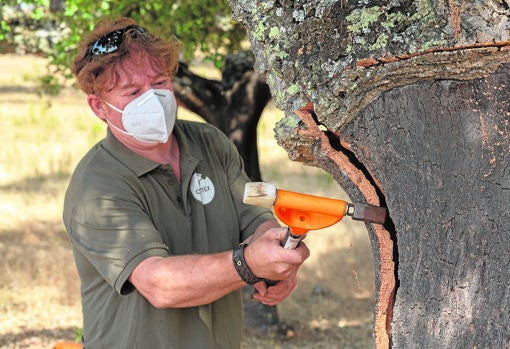
La fertirrigación supone otra innovación. Hasta ahora la repoblación se realizaba en secano, en el ámbito natural del alcornoque. Por una casualidad se descubrió que los alcornoques podían desarrollarse mucho más aprisa si hay agua que en su ciclo natural . «Mientras que en las repoblaciones tradicionales se tarda 25 años en descorchar por primera vez el alcornoque, con este sistema puede hacerse cada ocho años», indica Santiago.
Ciclo lento
En el ciclo del alcornoque, hasta la tercera pela no se obtiene corcho apto para hacer tapones, advierte el técnico en Subericultura: «En Extremadura, el término medio para el primer descorche se hace con 37 años, el segundo con 46 y el tercero, cuando empiezas a tener corcho de buena calidad, con 55 años».
Joaquín Herreros de Tejada , presidente de Asecor-Cluster del Corcho, apuesta por dinamizar el sector para que mejore la producción : «Tenemos que tomar medidas para que la producción no decaiga. Porque es una dinámica lenta, tanto que resulta difícil investigar».
Conforman Asecor (Agrupación Sanvicenteña de Empresarios del Corcho) distintas empresas del sector en todos los eslabones de la cadena de valor del producto. Esta organización ha impulsado la Plataforma Tecnológica Española del Corcho. Herreros de Tejada estima que «el sector ha evolucionado enormemente en los últimos veinte o veinticinco años. El tapón de corcho es el que aporta más valor añadido al sector . Cada año se venden en torno a 12.500 millones de unidades de tapones. Un 65% de los vinos del mundo se tapan con corcho».
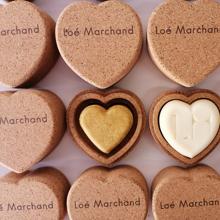
Algunas empresas se han apuntado a cambiar la historia del corcho. Un ejemplo es Corkup , una compañía radicada en Sevilla que nació con la pretensión de innovar en el mundo del corcho, de cambiar una historia muy ligada al tapón. Su responsable, Álvaro Granados , visibilizó las posibilidades del producto como material de accesorios de moda: « Con el grano de corcho se pueden realizar envases y accesorios para cosméticos sólidos . También se utiliza en decoración o en hostelería, para fabricar menús con tela de corcho».
Álvaro Granados valora especialmente la sostenibilidad de este producto: «Se trata de un material procedente del alcornoque, que se encuentra fundamentalmente en el Mediterráneo. No nos tenemos que ir a buscar la materia prima muy lejos Su origen, su valor natural, su proceso de fabricación… al final la huella de CO2 que deja es negativa».
Noticias relacionadas